By Abhishek Singh
Featured Photograph courtesy of Aradhita Parasrampuria
Innovating in sustainable fashion, Aradhita Parasrampuria combines her Indian heritage with creative materials design. Moved by the environmental impact of the fashion industry, she is dedicated to creating ethical, affordable, and eco-friendly materials. Using synthetic biology, she has developed sustainable dye production techniques and created biodegradable textiles from renewable resources like algae. Her project, Cellsense, features biodegradable, algae-based embellishments, signifying an essential step towards a more responsible fashion industry.
We recently spoke to Aradhita Parasrampuria, who is transforming the fashion industry with her sustainable materials design. We delved into her journey from India to New York, the inspiration behind her work, and how she’s reshaping fashion with a focus on environmental responsibility. She also shared insights into her innovative work and her future plans.
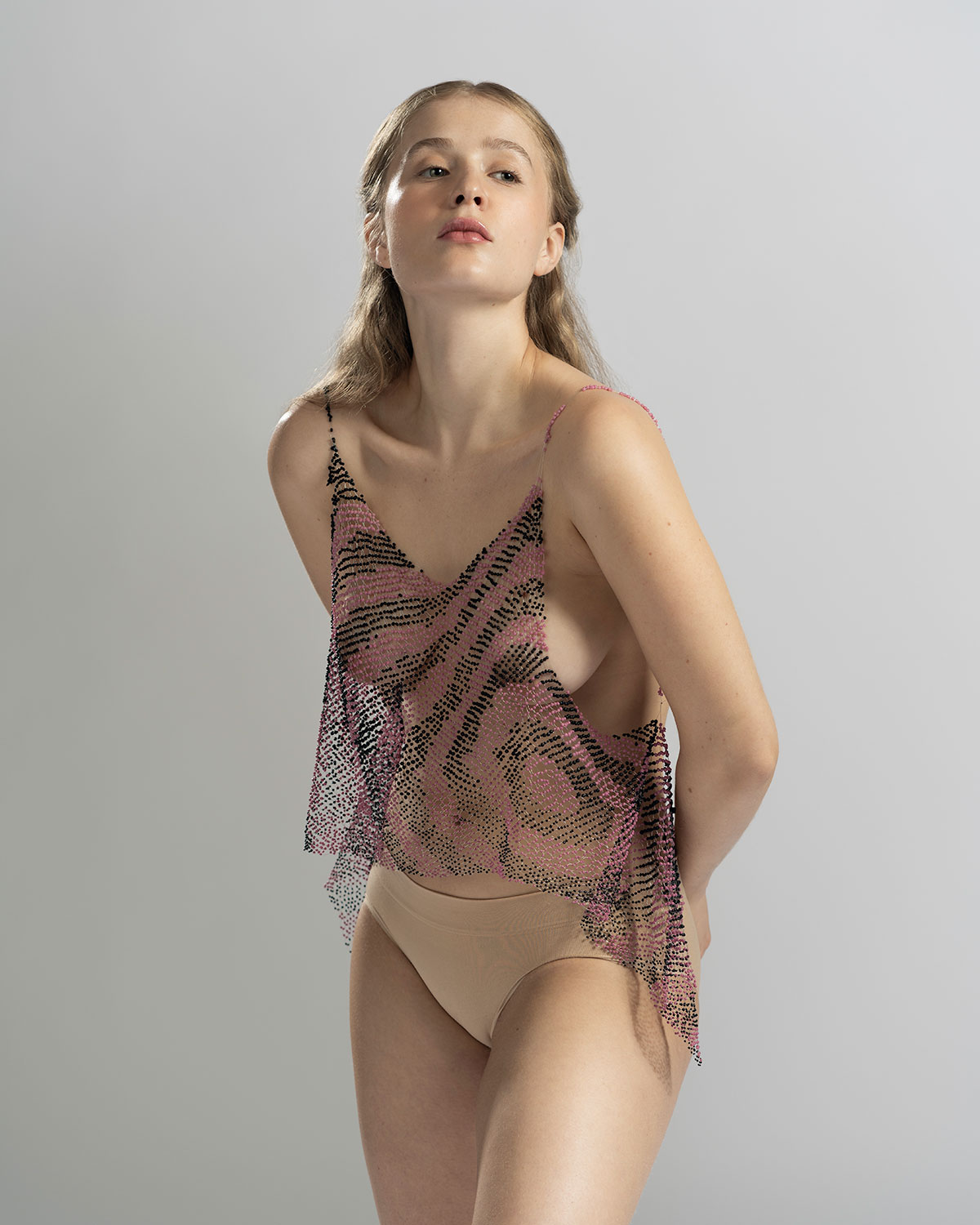
Photograph by Kuan Hsieh
Aradhita, can you tell us a little about your journey from India to New York and how your cultural background has influenced your work as a materials designer and fashion innovator?
Moving from India to New York at 17 to attend Parsons School of Design was a significant shift for me. The fashion industry in New York was exciting, but I was taken aback by its exploitative and wasteful nature. I was raised in Gujarat, a major textile hub in India, and was accustomed to a deep respect for the craft and production of textiles. This contrast inspired my interest in materials and their sustainability. It made me question the industry’s go-to “sustainable” options such as organic cotton and natural dyes, which are still quite resource and labor-intensive. In response, I started looking into ways to incorporate nature’s efficiencies into textile production. This journey, blending my cultural heritage with my drive for innovation, continues to shape my work as a materials designer.
Your work revolves around creating biodegradable materials and sustainable fashion. What was the turning point for you to focus on sustainability in your career?
The turning point towards sustainability in my career came after my first year at Parsons. I spent that summer working in a textile factory in my hometown, Ahmedabad, hoping to learn more about garment production and textile dyeing. The experience was eye-opening, to say the least. Workers were routinely exposed to hazardous chemicals from synthetic dyes, leading to serious health issues such as dermatitis and asthma. The wastewater, filled with toxins, was regularly dumped into nearby rivers, affecting local agriculture and marine life.
These disturbing insights made me realize that I could no longer work in an industry that operated in such a reckless manner. I felt pushed to develop sustainable materials and production methods that are chemical, allergen, and pesticide-free, and non-toxic to consumers and producers alike.
As part of this effort, I have developed a closed-loop, carbon-neutral embellishment system that uses algae and regenerated cellulose derived from textile waste. By leveraging the unique properties of the biopolymer, I have automated the production process to create large-scale beaded panels in a cost, labor, and time-efficient manner. This approach not only reduces the burden on textile industry workers who often suffer from carpal tunnel syndrome due to constant repetitive hand movements but it also helps ensure that sustainability is economical and does not remain a luxury.
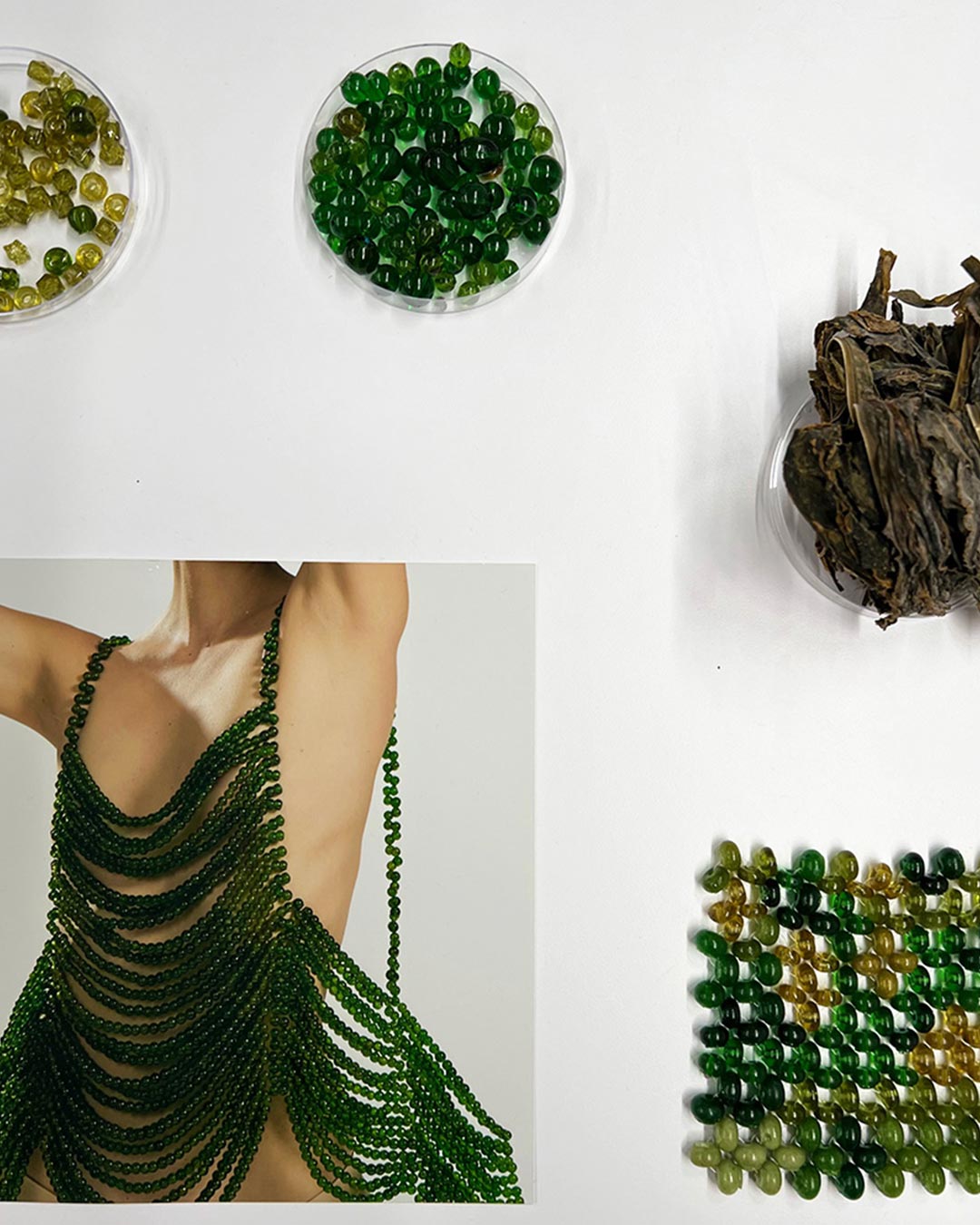
Photograph by Kuan Hsieh
How do you ensure that your materials are not only sustainable but also ethical and affordable, given the challenges in the fashion industry?
Creating sustainable, ethical, and affordable materials in the fashion industry is indeed a complex challenge. The industry’s impact on water scarcity is staggering – the production of a single cotton t-shirt, for instance, can consume up to 2,700 liters of water. This is a pressing concern, considering over 2 billion people worldwide grapple with water scarcity.
In addressing this, I firmly believe that a comprehensive approach is necessary, one that addresses every stage of the supply chain. Although recycling and using materials like cotton are valuable steps, they alone can’t resolve the high resource consumption in the fashion industry.
To tackle this, my work involves combining fashion with synthetic biology, fostering the creation of biodegradable materials from renewable resources such as bacterial cellulose and algae. These materials are resource-efficient, requiring up to 99% fewer resources than petroleum products.
Can you share with us one of your past projects that had a significant impact on your career and how it shaped your current work?
The project that really stood out to me was when I first experimented with synthetic biology in fashion. I had this idea: could we use bacteria as a sustainable dye source? After three months of trial and error, I finally managed to engineer a bacteria that produced an iridescent blue dye.
This project was a turning point for me. Not only did I end up with a far more water-efficient dye than synthetic options, but the process made me privy to the potential of biodesign. That project drove me to learn more about synthetic biology and biochemistry, and it has significantly shaped my current work in creating sustainable and biodegradable materials for the textile industry.
In your project, Cellsense, you have created a collection of pieces utilizing biodegradable algae-based embellishments. Can you share more about the inspiration behind this project, and how it has been received by the fashion industry and consumers?
The inspiration for “Cellsense” emerged from an urgent and unaddressed challenge within the design industry: the lack of sustainable and ethical alternatives to conventional plastic and synthetic resin-based embellishments. This concern is not trivial; the global embellishment market stood at a staggering 23 billion USD in 2021, with the costume jewelry market trailing closely behind at $32.9 billion in the same year. Alarmingly, synthetic garments contribute to 35% of the ocean’s microplastics, with embellished garments typically discarded after a mere five wears.
Using algae and cellulose as a basis, we create 100% biodegradable and renewable embellishments which we design to be easily molded for scalable impact. Our products can react to their environment and create an interactive consumer experience. Beyond broad environmental benefits, it also eliminates physical hazards for textile workers.
Sustainable embellishments available in the market are made from PET, which is costly and difficult to biodegrade, while ours requires no special processing. We have also added engaging features such as bioluminescence or transforming colors, which created an enhanced experience for the user.
Cellsense was born out of my college thesis project and scaled up thanks to the “Creatives For Our Future” initiative by the Swarovski Foundation and the UN. This opportunity helped establish Cellsense LLC, apply for patents, and piqued the interest of sustainability-focused fashion brands even before product commercialization. Customers and designers often liken the feel and aesthetics of our green beads to gemstones such as jade or emerald. This reinforces our commitment to creating a product that marries environmental responsibility with beauty.
You have worked with various organisms like Kelp, Escherichia coli, and Mycelium in your projects. Can you elaborate on the role of these organisms in creating sustainable textiles and what makes them ideal for your work?
Kelp, E. coli, and Mycelium are fascinating organisms that offer a range of possibilities for sustainable textiles.
Kelp, for instance, is a type of seaweed that grows rapidly and absorbs carbon dioxide from the atmosphere. This renewable resource can be harvested without inflicting harm on the ecosystem. In addition, kelp cultivation can provide fishermen with alternative income sources during their off-season, enhancing local economies while promoting environmental sustainability.
E. coli, a common bacterium, can be ingeniously engineered to produce vibrant dyes and proteins that emulate the feel of silk.
Mycelium, the root structure of mushrooms, can be grown into dense, 3D structures and leather-like material. All of these organisms can be grown under controlled conditions with minimal resource input, making them ideal for sustainable textile production
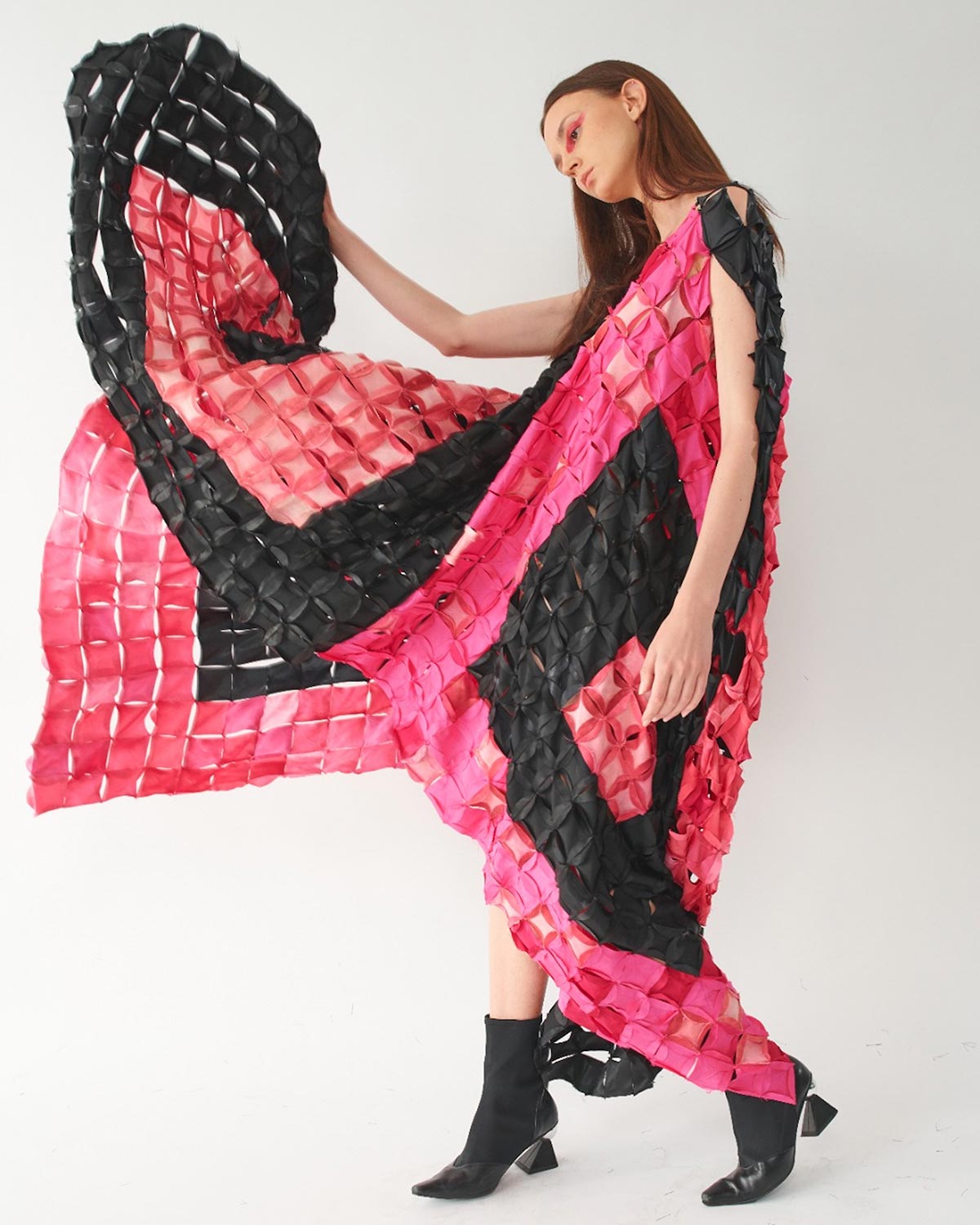
Photograph by Jamie Pavon
What are some of the challenges you have faced in the development of your innovative materials, and how did you overcome them?
Biopolymer embellishments haven’t been fully developed yet and there is a complete lack of resources or literature we can reference for this process. We are one of the first to figure out material composition and development, scaling up, and life cycle testing for this kind of product, which was both exciting and challenging. We are determined to remain true to our values and refrain from including harmful synthetic additives in our products. Instead, we focus on using resources that are naturally abundant and affordable.
I believe that economical production is also a requirement so we can replace conventional embellishments, ensuring that sustainability doesn’t remain a luxury item. To pursue this, we use an automated pipetting system called Opentron to allocate biopolymers at divots on a 3D-printed bead loom, creating large-scale customizable beaded panels in a time, labor, and cost-efficient manner. By harnessing the unique properties of biopolymers and employing innovative production methods, we offset expenses associated with biopolymer use, making these sustainable materials economical while also reducing the burden on workers who often suffer from carpal tunnel syndrome due to constant repetitive hand movements.
And in terms of aesthetics, we have integrated a protein extracted from jellyfish called “Aequorea victoria” into our biopolymers, making the material bioluminescent and offering unique design possibilities to both designers and consumers. This innovative approach allows us to demonstrate the versatility and appeal of biodegradable materials, ultimately shifting perceptions within the industry.
What can we expect to see from you in the future? Are there any upcoming projects or collaborations that you are particularly excited about?
Currently, we’re thrilled to be collaborating with two jewelry designers, one based in the US and another in India. We’re also partnering with a sustainability-focused fashion brand based in New York, all with the aim of creating innovative designs using Cellsense materials. We look forward to the launch of these designs soon!
While many biotech companies focus on developing materials for future applications, our approach emphasizes creating products that can be embraced by customers in the present. We are committed to driving positive change in the industry and delivering sustainable, modern options for consumers today.
Finally, are there any designers, artists, or innovators who have inspired your work or whom you think our readers should know about?
There are many talented and innovative individuals out there, but some of my key inspirations include:
Natsai Audrey Chieza: Founder of Faber Futures, Natsai is a pioneer in the field of biodesign. Her work fuses biology, design, and sustainability, and she’s recognized for her innovations in bacterial dyeing processes.
Céline Semaan: A designer, writer, and advocate, Céline is the founder of Slow Factory, a nonprofit organization dedicated to improving environmental and human rights issues in the fashion industry. Her work merges activism with fashion, proving that style and sustainability can go hand in hand.
Tessa Callaghan: Co-founder of AlgiKnit, a biomaterials company integrating algae-based yarns into the textile industry. Callaghan’s work merges biodesign, sustainability, and fashion to create regenerative solutions.
Jasmina Aganovic: President of Ginkgo Bioworks, a bioengineering company developing custom microbes for a variety of industries. Aganovic is a key figure in the biotech space, exploring the potential of synthetic biology for sustainable production.